- August 9, 2019
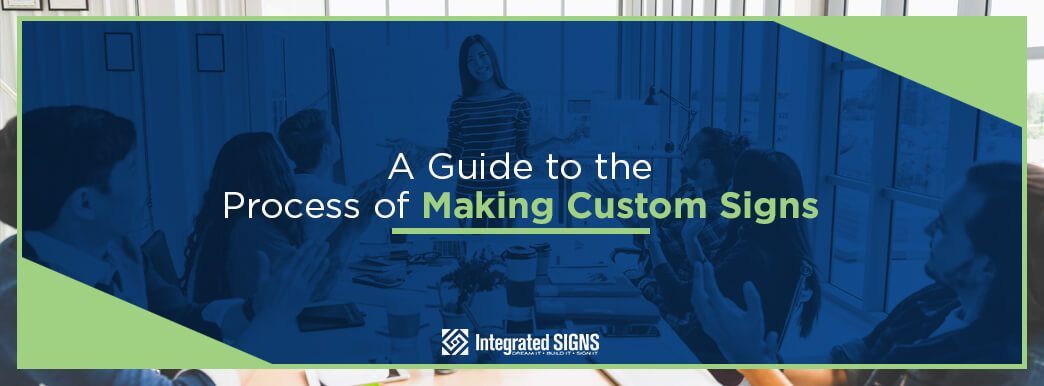
A Guide to the Process of Making Custom Signs
A custom sign sets your business apart from the rest. It conveys the purpose and brand of your company, catches the attention of potential customers and guides them to your building. But what is the process of ordering and making a custom sign?
The signage fabrication process varies depending on the sign and materials used. In general, the process when you order a product with a sign company is the same. You and the sign company will go through a process that includes:
- Consultation
- Designing concepts and mock-ups
- Obtaining a permit
- Sign manufacturing
- Sign installation
In our guide to the process of making custom signs below, you’ll find a breakdown of these steps. Read on to get a better understanding of the sign manufacturing industry before you order your custom signs.
What Is the Consultation Process With a Sign Company?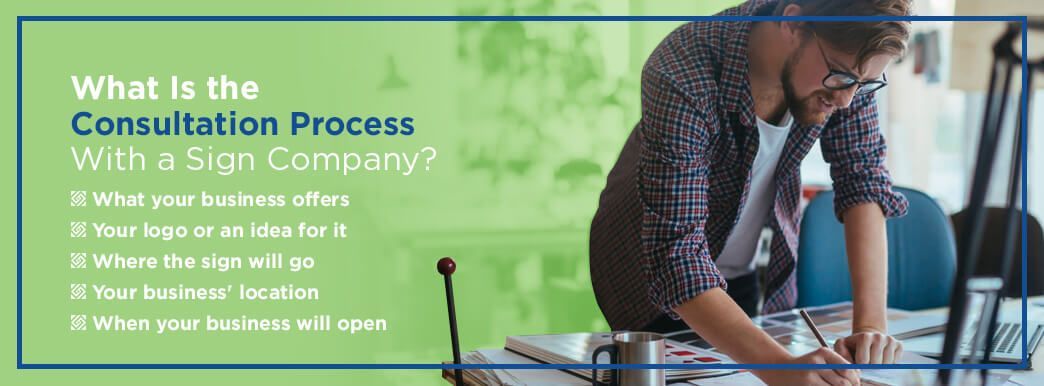
As you begin a custom business sign project with a company, you’ll go through a consultation process. In this process, sign manufacturing companies need a variety of information to create the best sign for your business. Some details you’ll need to provide can include the following.
- What your business offers: The products or services you provide can guide the sign fabrication process. Your industry may dictate what tone your custom signs convey. Education and banking businesses will want a clean, professional-looking sign. Design firms and small businesses may get a bit more creative with a custom architectural sign, while still maintaining a professional appearance.
- Your logo or an idea for it: The image, style and colors in your logo will help a sign company make a sign that reflects your brand. If you don’t have a logo yet or you’d like a new one, a full-service sign company will help you come up with one. A designer can integrate your logo into your signage, especially if it is an outdoor sign. They will choose a font and color scheme for your sign that best reflect your logo.
- Where the sign will go: Whether you want your sign outdoors or indoors, a designer will need to know the location. From there, they’ll suggest what materials and construction would work best for where you’d like the sign. If your sign will go inside, a designer will recommend different types of signage — such as lobby, reception or directory signs — that are different from outdoor signs. The architecture of your building also guides a designer’s vision for your signage, since you don’t want the product to clash with your property.
- Your business’ location: The location of your business determines different factors about your sign. The varying weather you experience will help a manufacturer pick materials that will last through various climates. If your business is off a main road, a designer will have different suggestions for what type of sign you should use than if you were on a main road. Monument signs, for example, work best for businesses that sit off on a side road. Your location also determines what codes your signage must meet, which we will explain in a bit.
- When your business will open: If your business is new or reopening, provide the opening date to the sign designer. This information gives them a timeline so they can work to deliver your signage when you need it.
With the above information, a sign designer can consult you on what signage you need, what designs are best for the signage and answers to any other questions you may have. From there, the sign design process begins.
How Do Sign Manufacturing Companies Design Signage?
After your consultation, a sign company takes your information and comes up with some designs for you. Depending on the designer, this process can involve a few steps.
- Concepts: A designer may create some rough ideas for you to check out based on any preferences you’ve identified. From there, you can select some of the concepts you think suit your business. Ask your sign designer for guidance if you aren’t sure which choices are best.
- Mock-ups: Some sign manufacturing companies offer digital mock-ups of your sign after you’ve chosen some concept designs. If you provide photos of your building where you’d like the sign to go, many designers can integrate a digital mock-up of their design into the photo. You’ll see how different signs could look in or on your building before one goes to manufacturing.
- Signing off: After you give feedback and the designer makes any adjustments, the final step of the design process is usually signing off on a project. With your go-ahead, the designer can move forward with your project.
After the steps above, a sign company may offer a proposal that details how much you can expect to pay for the project. Companies will calculate this number to the best of their ability. They take factors into account such as the materials they’ll use and the size of your sign. With a proposal, you and the sign company can work together to create something within your budget.
In addition to tailoring a budget for you, a designer will follow different specifications you provide to create an eye-catching sign for your company. Whether you have a creative eye and offer input on your design or if you feel you’re a non-creative type, a sign design company will help your signage come to life. Even if you do have an idea for your sign, you should work with a design company. A professional will ensure your company’s sign design includes:
- A legible font
- High-contrast colors
- Appropriate style and tone
- Useful information
- The right amount of words — between two and seven
- Materials that will last
The design aspects above will ensure your sign is eye-catching, but also that potential customers can still read it. You must also be able to put up your sign for individuals to see it. To do that, you must acquire a permit.
What Is the Permit Process for Indoor and Outdoor Signs?
Depending on where your business is, you’ll have different building codes to meet. Adding certain signs to your building is no exception. Some sign manufacturing companies will guide you through the permit process, and others complete it for you. Sign permits usually have regulations on factors such as:
- The size of the sign
- Where you can hang it
- How you have to hang it
Sign manufacturing companies need to know permit specifications before they begin the signage fabrication process to avoid having to make adjustments after the fact. You wouldn’t want to wait eagerly for a designer to fabricate a sign, only to realize it is not up to code. Acquiring a permit first will guide the process so the company makes your sign right the first time.
While the specifics of acquiring a permit for your custom business sign project vary across different cities, you may have to submit the following.
- Permit fees: Some general fees cover the costs of mapping, records and planning. You’ll find out what specific expenses you have to include in your application process.
- Inspection fees: The type of sign you’d like determines whether or not you pay an inspection fee. Wall signs, especially those on high-rises, and lit signs may require inspection in your city.
- Applications and other plans: You will likely have to fill out a permit request form, or a full-service sign company may walk you through this process and help you complete it. You may also have to submit site and elevation plans along with paperwork that verifies your ownership of the building.
Once you or the sign company provides the necessary submissions, the length of time it takes to get a permit application approved depends on variables such as:
- Your location and its individualized process
- If your business is in a historical building
- The type of sign you’d like to install
Some signage does not require permits, such as some interior signs, non-illuminated construction and real estate signs, memorials integrated into a building and other signs. It’s best to check with your sign company and your city to determine if your project requires a permit. After your city approves your sign permit, the sign fabrication process begins.
How Are Custom Signs Made?
The custom signs you choose change the manufacturing process and materials a designer uses. Many manufacturers use high-quality materials that are made to last through any weather for years to come. While you could find cheap and affordable commercial signs with a print shop, they aren’t guaranteed to last like a sturdy, professionally made sign. Below you’ll find some of your signage options and how a manufacturer creates them.
- Channel letters: These are typically outdoor signs made of individual characters. A sign manufacturer makes separate letters and numbers, usually out of aluminum and acrylic. Channel letters come in face-lit varieties, where designers include internal lighting to illuminate the characters. Reverse or halo-lit options light up from the back, projecting light onto your building in a soft glow. Channel letters appear on storefronts and high-rises alike and are an eye-catching sign option.
- Blade signs: As one of the most popular varieties of signage, blade signs stick out from the side of a building to flag down potential customers. Manufacturers will construct the sign and a mounting system, which can feature a simple pole and frame or a decorative bracket. Sign manufacturing companies may offer lit or unlit versions, and can construct a blade sign that suits your building and brand. Designers can build blade signs with a variety of high-quality materials.
- Interior lobby or reception signage: Interior signs include displays above a reception desk or somewhere in your lobby. These signs usually display your business name and come in a range of styles, colors and materials. A manufacturer will produce an illuminated or non-illuminated interior sign, depending on your preference.
- Monument signs: These larger and eye-catching signs are best for companies in business parks or set back from the main road. Designers often incorporate architectural aspects of the building into the sign they make, from the color to the general style. Monument signs usually include brick, stone or other sturdy materials for the base. Information like the name of your business and the address will appear on the sign.
- Code signage: Code signage must meet specific requirements, according to the Americans with Disabilities Act. When manufacturers create code signage for your business, they ensure it is simple to read, both visually and to the touch with Braille and raised lettering.
- Neon signs: As one of the most classic signage options, a neon sign evokes a vintage feel. Every neon sign is unique because of its construction process. A manufacturer must bend glass tubing to create each letter, number and shape in your sign. They mount the glass on a framework made of a sturdy material after filling the tubing with the gas that allows the sign to light up in the color you choose.
Above are some potential custom business sign projects, but the company you choose may offer other options. In your consultation, a sign company may recommend certain signs, particularly if you’re a new business and need several projects. From there, they take your company’s sign design and make it a reality. Once a manufacturer completes the sign, it’s time to install it.
What Is the Installation Process for Custom Signs?
A full-service company sign design provider will offer installation of your new sign. While some sign manufacturing companies may only service local areas, you can find a sign company that provides installation for businesses across the country. Similar to the signage fabrication process, installing a sign depends on the type you’ve selected. Sign companies may have to install individual characters or sections of a sign, secure brackets and mounting or other complex aspects of signage before the project is complete.
If you have to look for a different installation company other than the one that created your sign — or as you look for a manufacturer in the first place — consider these tips:
- Choose an insured, professional installation company.
- Find a company that specializes in installing signs or even the type of sign you’ve selected specifically.
- Be sure the company surveys the building to formulate a plan.
- Ensure the sign company has many years of experience.
- Check out past client testimonials to choose the most reliable company.
- See if the installation company is familiar with your industry so they can treat you with professionalism.
A trustworthy installation company should do everything they can to be sure they have installed your new sign safely, securely and correctly. They should use up-to-date machinery and tools while following local building codes and permit regulations.
Why Choose Integrated Sign Associates for Your Custom Sign Projects?
As we walked you through the signage fabrication process and gave you insight into the sign manufacturing industry, you may have realized your business’ need for new signage. Integrated Sign Associates would be pleased to be your choice for your company’s sign design. Our range of signage products is sure to meet any need, whether you’re a new company or you’re interested in replacing your current signs with high-quality options.
ISA offers professionally made products and creative sign designs. As a full-service sign company, we walk you through the consultation, design, permit acquisition and installation. Contact us online or at 619-579-2229 when you’re looking to upgrade your business and draw in more customers with our eye-catching signs.